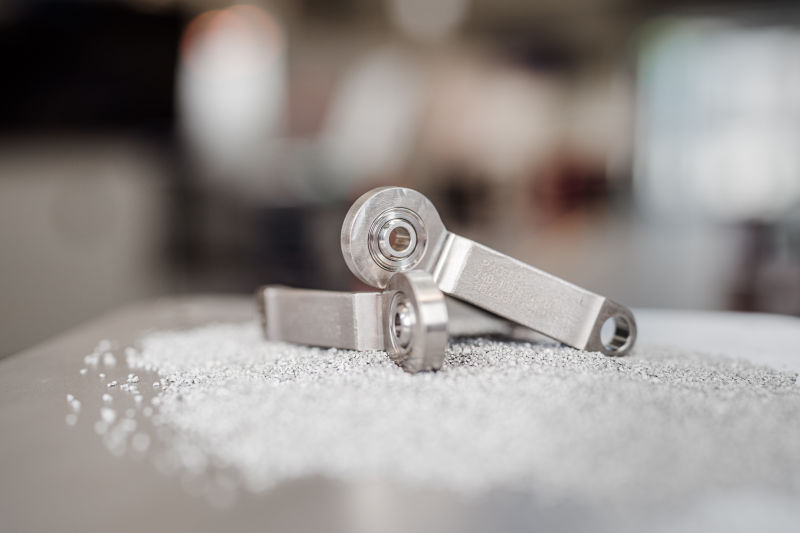
En su esfuerzo conjunto por utilizar métodos de fabricación aditiva para una producción de piezas de repuesto para aviones más rentable, Lufthansa Technik y Premium AEROTEC alcanzaron recientemente un hito importante: un componente de metal desarrollado en el Centro de Fabricación Aditiva (AM) de Lufthansa Technik para el motor IAE-V2500. El sistema antihielo ahora ha recibido su certificación oficial de aviación de EASA. Sobre esta base, Premium AEROTEC producirá el llamado «A-Link» para Lufthansa Technik en su sitio de Varel (Alemania) utilizando una impresora 3D.
Un total de nueve de estos A-Links fijan un conducto de aire caliente en forma de anillo en la cubierta de entrada del motor, que queda así protegida de la acumulación de hielo durante las operaciones de vuelo. Sin embargo, las vibraciones que se producen aquí durante el funcionamiento hacen que los enlaces A se desgasten en sus orificios de montaje, por lo que, después de unos años, suelen estar listos para ser reemplazados.
Como los A-Links pueden estar expuestos a temperaturas de hasta 300 grados centígrados, están hechos de titanio. En el original, el componente se fabrica mediante un proceso de forjado para cumplir con los más altos requisitos de propiedades del material. En la nueva solución de fabricación desarrollada por Premium AEROTEC y Lufthansa Technik, sin embargo, se construye capa por capa en una impresora 3D. Este proceso, llamado Laser Power Bed Fusion (LPBF), ofrece la ventaja sobre el forjado de que no se necesitan plantillas ni moldes para la producción. Además, el proceso puede ahorrar material valioso, ya que después de la impresión 3D solo es necesaria una eliminación de material muy pequeña en algunas superficies funcionales.
Sin embargo, las propiedades de los componentes producidos de esta manera, por ejemplo, su resistencia, dependen en gran medida del correspondiente proceso de fabricación aditiva, cuya calificación, por lo tanto, debe probarse en un procedimiento complejo. Con este fin, Premium AEROTEC realizó una gran cantidad de los llamados «trabajos de impresión» con muestras de prueba, con ajustes constantes de todos los parámetros relevantes para el proceso. De esta manera, finalmente fue posible establecer un proceso constante y confiable y demostrar que aquí también se logran los más altos requisitos en términos de propiedades del material. En términos de resistencia a la tracción, el A-Link fabricado aditivamente es incluso superior a la pieza original.
Como parte de este proceso de certificación, Lufthansa Technik ha ampliado la experiencia de su centro de desarrollo EASA Parte 21/J para incluir componentes metálicos fabricados de forma aditiva. Para Premium AEROTEC, la cooperación con Lufthansa Technik es un hito importante en el campo de la fabricación aditiva, ya que es la primera vez que la empresa suministra componentes de series impresas a un cliente fuera de Airbus Group. Los primeros A-Links de la cooperación se utilizarán en la flota de Lufthansa, donde se obtendrá una experiencia a largo plazo con los nuevos componentes más allá de la certificación.
«Premium AEROTEC es pionera internacional y líder tecnológico en la fabricación aditiva de componentes aeroespaciales. Nuestra empresa ya aplica esta tecnología en la producción en serie de componentes estructurales complejos desde 2016», dijo el Dr. Ulrich Weber, director de operaciones de Premium AEROTEC. . «Estoy muy contento de que, en cooperación con Lufthansa Technik, ahora podamos demostrar una vez más nuestra amplia experiencia en impresión 3D».
«Hemos estado produciendo componentes para la cabina de los aviones, la gran mayoría de los cuales están hechos de plástico, usando impresión 3D durante años. Ahora podemos demostrar que las piezas metálicas estructuralmente relevantes para usar fuera de la cabina también pueden fabricarse de forma aditiva y aprobarse». para las operaciones de vuelo», dijo Soeren Stark, director de operaciones de Lufthansa Technik. “De esta manera, no solo hemos logrado un ahorro de costos para el componente en cuestión, sino que también hemos definido y calificado todos los procesos necesarios para la aplicación de este método de fabricación innovador para piezas metálicas estructuralmente relevantes”.
Sin embargo, la primera certificación aeronáutica de una pieza de repuesto metálica de carga representa actualmente solo un primer paso para ambos socios, ya que su geometría aún se corresponde en gran medida con la pieza original. Los futuros desarrollos en la tecnología también permitirán utilizar las ventajas de la fabricación aditiva para la optimización específica de la geometría. Teóricamente, no existen límites para la conformación de componentes fabricados de forma aditiva, por lo que se pueden producir mucho más fácilmente y con menos material conservando la misma resistencia y función. Ambos socios tienen la intención de seguir desarrollando estas posibilidades en un futuro próximo.
Lufthansa Technik/Junio 08 de 2022