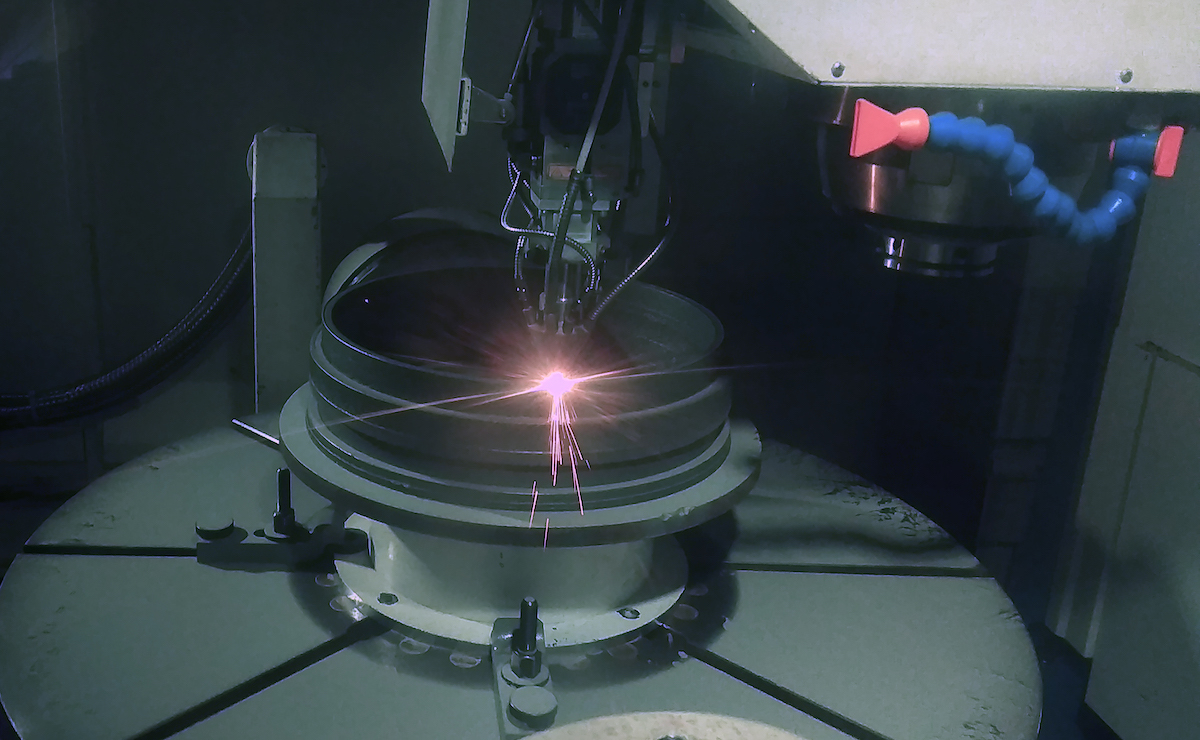
La United Engine Corporation (UEC) de Rostec State Corporation ha desarrollado el primer complejo híbrido de 5 ejes en Rusia para la producción de piezas experimentales para motores de turbina de gas. El centro de mecanizado CNC combina impresión 3D, mecanizado y soldadura láser. La máquina ya está produciendo piezas complejas de gran tamaño para las necesidades de la UEC.
El desarrollo no tiene análogos en términos de sus características técnicas y capacidades tecnológicas. El complejo está diseñado para la producción a alta velocidad de piezas de gran tamaño de perfil complejo para motores de turbina de gas mediante el método de crecimiento láser directo y procesamiento mecánico. A diferencia de los análogos extranjeros, permite la producción y procesamiento de alta precisión de piezas de gran tamaño para motores de turbina de gas con dimensiones de hasta 1100x600x600 mm y un peso de hasta 450 kg.
Se desarrolla un programa de control individual para cada pieza, que se crea sobre la base de un modelo de diseño 3D. Primero, la pieza de trabajo se cultiva a partir de polvos metálicos especiales resistentes al calor. Luego, el complejo realiza automáticamente el torneado y el fresado, lo que le permite obtener una pieza completamente terminada en la salida.
“El complejo digital combina las funciones de una impresora 3D y varias máquinas de procesamiento, lo que puede reducir significativamente el tiempo de desarrollo y lanzamiento al mercado de nuevos motores de avión. Una máquina híbrida en pocas horas crea una pieza a partir de un modelo digital tridimensional, que tarda varios meses en fabricarse de forma tradicional. Esta tecnología también abre amplias perspectivas de cooperación entre las empresas del clúster de aviación de Rostec. El nuevo equipo se utilizará para producir piezas experimentales y realizar trabajos encargados por otras oficinas de diseño. Ya se está trabajando para cumplir con los primeros pedidos”, dijo Vladimir Artyakov, primer subdirector general de Rostec.
Debido a la alta potencia del láser de fibra – 3 kW – el complejo puede soldar hasta 6 mm de espesor. El complejo híbrido también se puede utilizar para reparar piezas dañadas.
“Estos complejos híbridos se están desarrollando solo en unos pocos países del mundo: Alemania, Japón, Corea y China. Pero son de menor tamaño en la producción de piezas de motor de avión de gran tamaño. Nuestros expertos, junto con nuestros socios, han encontrado una solución única que elimina las restricciones existentes”, dijo Sergey Pavlinich, director de la rama de United Engine Corporation JSC“ Instituto de investigación de tecnología y organización de la producción de motores ”(JSC UEC“ NIID”).
El proyecto se implementó en la sucursal de JSC «UEC» «NIID» (Moscú) por orden de JSC «UEC» en cooperación con la Universidad Politécnica de San Petersburgo y LLC SKB «Stankostroenie» (Sterlitamak).
Rostec/Agosto 21 de 2020